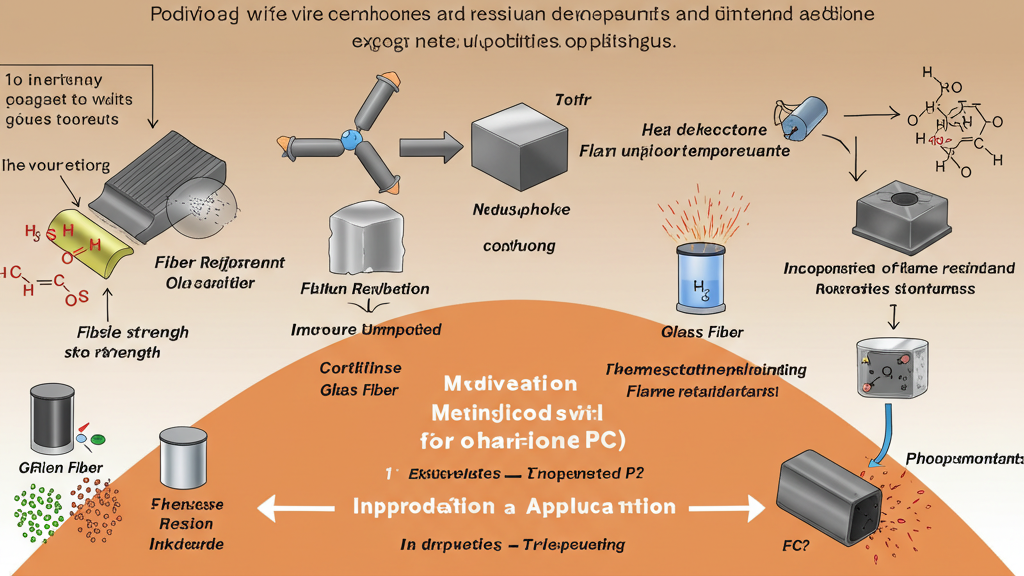
Polycarbonate (PC), with its high strength, high transparency, and impact resistance, has become an important engineering plastic. Extrusion molding is a crucial process for turning PC pellets into various profiles. Precise control of extrusion process parameters directly affects product performance and application range. This article will explore the PC extrusion process, key factors, and its wide range of applications, providing a professional reference.
We will focus on the core aspects of PC extrusion molding. From raw material pretreatment to process parameter settings, each step is critical. In view of the characteristics of PC, special techniques and additives are often used in the extrusion process to improve processing performance and product quality. These will lay the foundation for subsequent discussions on its application fields.
Why does polycarbonate typically require pretreatment?
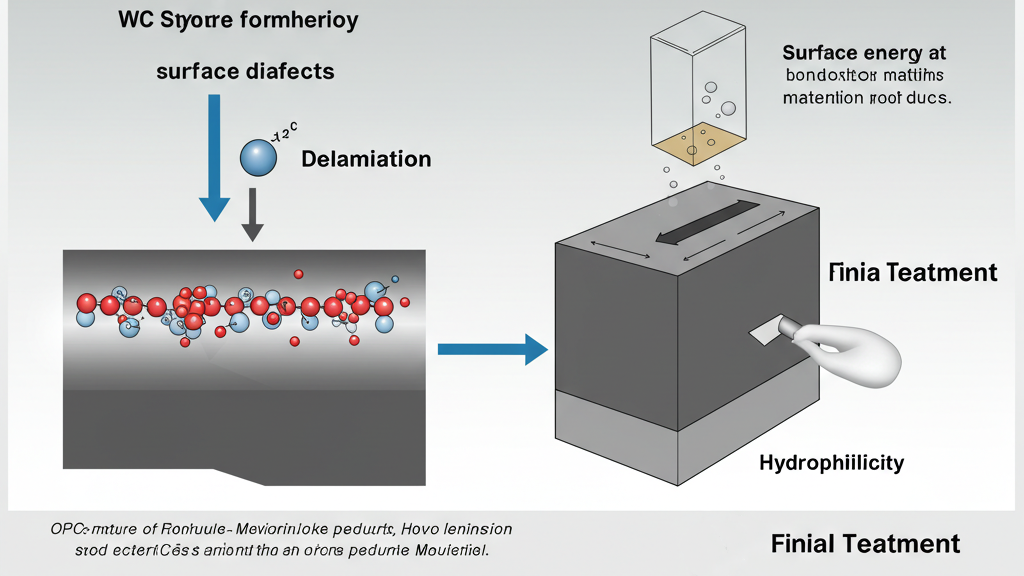
The presence of ester groups in the polycarbonate molecular chain makes it relatively sensitive to moisture. During high-temperature melt extrusion, even trace amounts of moisture can trigger hydrolysis reactions, significantly reducing the material’s molecular weight and mechanical properties. Therefore, pretreatment is a crucial step to ensure the quality of extruded products.
- Suppressing Hydrolysis Reaction: Pretreatment removes moisture, preventing the breakage of polycarbonate molecular chains during high-temperature extrusion, thereby guaranteeing the material’s mechanical properties.
- Reducing Defect Formation: Drying treatment prevents moisture from vaporizing during extrusion, which can cause bubbles and surface defects, enhancing the product’s visual quality.
- Ensuring Processing Flowability: Pretreatment ensures the stability of polycarbonate in the molten state, improving the uniformity and molding efficiency of extrusion.
- Enhancing Final Product Performance: Thorough drying helps polycarbonate maintain its excellent properties after extrusion, meeting application requirements.
How do extruder types and screw designs affect extrusion quality?
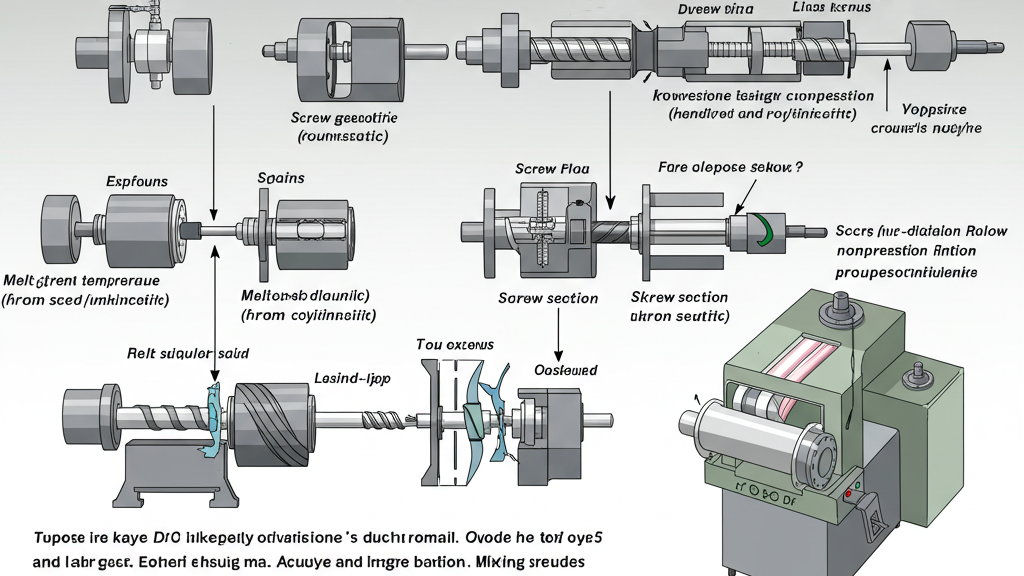
The extruder, as the core equipment for polycarbonate extrusion molding, directly determines the plasticization effect of the material, the stability of melt conveying, and the final product output. The screw, as a crucial component of the extruder, its geometric parameters and design directly affect the mixing, shearing, melting, and venting efficiency of the polycarbonate, thereby significantly influencing the quality of the extruded products.
- Extruder Type: Different types of extruders determine the plasticization and mixing efficiency of polycarbonate, affecting the uniformity of blend-modified products.
- Screw Design and Conveying: Reasonable screw geometry ensures stable and uniform melt conveying, reducing product size deviations.
- Screw Design and Shear Temperature Control: Optimized screw structure and rotation speed control shear and temperature rise, preventing polycarbonate degradation and ensuring plasticization quality.
- Vented Screw: Using a vented screw design can effectively remove volatiles and moisture from the polycarbonate, reducing product defects.
What are the common product forms of polycarbonate?
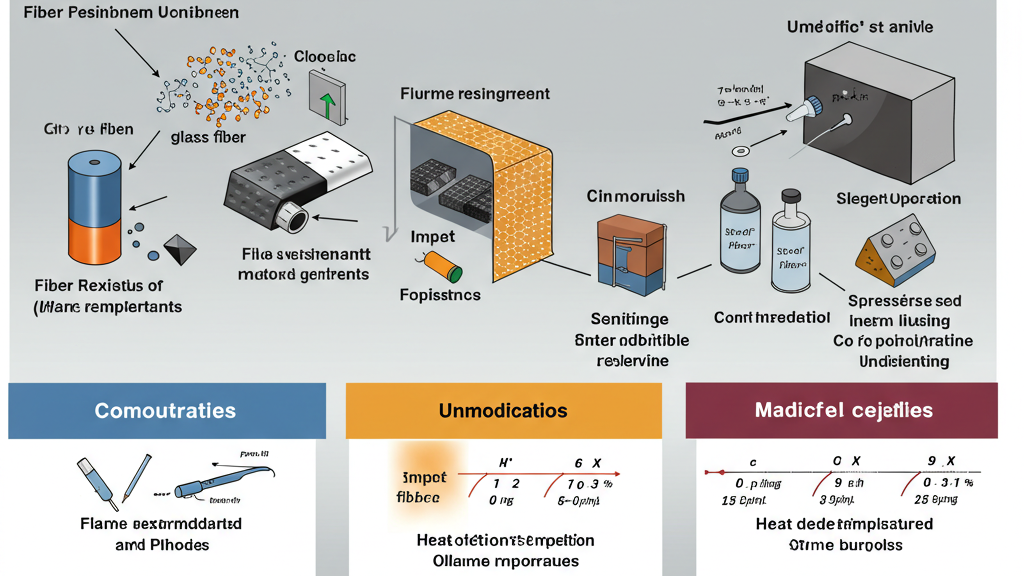
With its excellent comprehensive performance and good processability, polycarbonate can be manufactured into a variety of product forms through the extrusion molding process, from sheets and plates to pipes, profiles, and even films, which are widely used in various industrial and consumer fields.
- Sheets and Plates: Polycarbonate sheets and plates, with their high transparency and impact resistance, are widely used in construction, advertising, and security applications.
- Pipes and Rods: Polycarbonate pipes and rods, due to their transparency and strength, are commonly used in medical devices, laboratory equipment, and mechanical components.
- Films and Sheets: Polycarbonate films and sheets, with their optical and mechanical properties, are used in electronics, packaging, and optical fields.
- Profiles: Polycarbonate can be extruded into various complex cross-section profiles to meet the special structural needs of industries such as electronics, automotive, and furniture.
Extrusion molding process guide and common products
Process Stage |
Key Control Parameters |
Common Issues |
Solutions |
Corresponding Common Products |
Raw Material Pre-treatment | Drying Temperature, Drying Time, Target Humidity | Hydrolysis, Bubbles | Optimize Drying Process, Control Raw Material Moisture | Sheets, Films, Tubing, Pipes |
Extrusion & Screw | Extruder Type, Screw Design, Barrel Temperature | Poor Plasticization, Degradation | Select Suitable Equipment, Optimize Screw Design | Various Profiles, Blended Modified Products, Transparent Products |
Die & Molding | Die Design, Die Head Temperature, Extrusion Speed | Deformation, Dimensional Inaccuracy | Optimize Die, Adjust Process Parameters | Sheets, Films, Tubing, Profiles |
Cooling & Sizing | Cooling Method, Cooling Temperature, Sizing Device | Deformation, Internal Stress | Optimize Cooling & Sizing Process | Sheets, Films, Tubing, Profiles |
Common Modification Methods and Additives
To expand its application areas and meet diverse performance requirements, common modification methods and additives play a vital role. By means of physical blending, chemical grafting, and other methods, specific properties of polycarbonate, such as heat resistance, impact resistance, flame retardancy, and weather resistance, can be significantly improved.
1.Reinforcement and Toughening Modification: Adding fibers or elastomers to enhance the strength, stiffness, and toughness of polycarbonate.
2.Flame Retardant Modification: Adding flame retardants to impart excellent fire resistance to polycarbonate, meeting safety requirements.
3.Weather Resistance Modification: Adding ultraviolet absorbers and other additives to improve the anti-aging ability of polycarbonate and prolong its service life.
4.Functional Modification: Adding various additives to give polycarbonate extruded products specific functions such as antistatic, conductive, or aesthetic properties.
Conclusion
With its excellent comprehensive performance, polycarbonate can be manufactured into various product forms through the extrusion molding process, widely used in multiple fields. To ensure high-quality extruded products, the pretreatment of raw materials is crucial, while the selection of the extruder and the optimized design of the screw directly affect plasticization, melting, and conveying efficiency.
For expert assistance in implementing for your production needs, visit our resource center or contact us. Let’s help you scale up your manufacturing with precision and efficiency!
Post time: Apr-21-2025